How DC Calibrators Ensure Precise Measurements
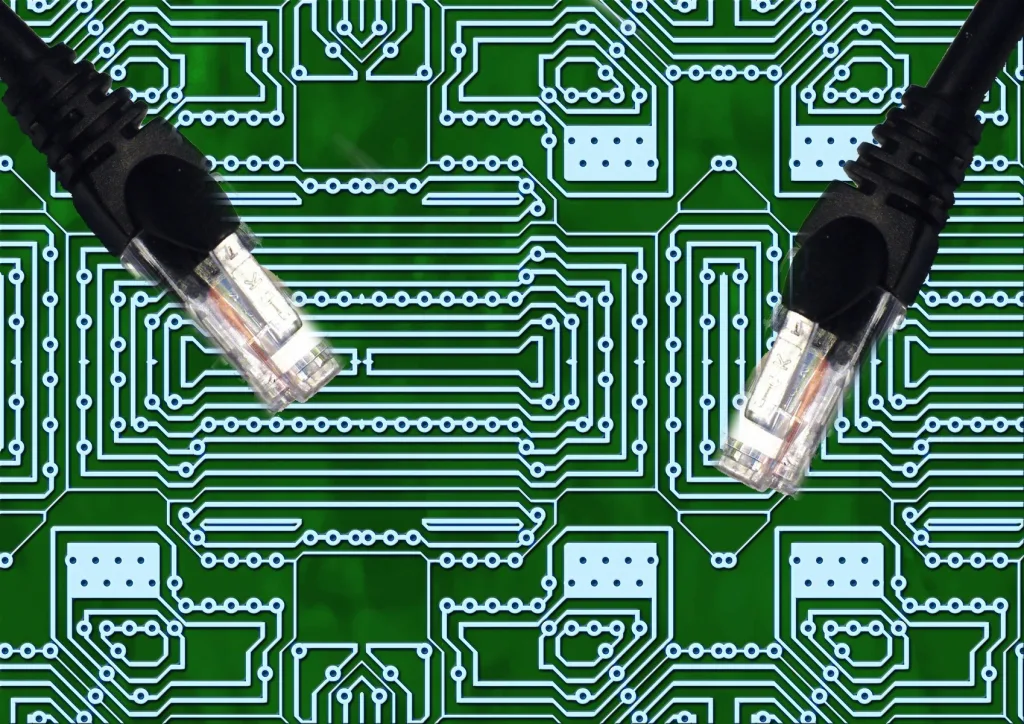
In the realm of electrical measurements and instrumentation, precision is paramount. Engineers, technicians, and scientists rely on accurate measurements to ensure the quality, safety, and performance of electronic systems and devices. One essential tool in achieving this level of accuracy is the DC calibrator. In this blog post, we will explore what DC calibrators are, how they work, and why they are crucial for ensuring precise measurements in various industries.
Understanding DC Calibrators
DC calibrators are instruments designed to generate and maintain precise direct current (DC) signals for calibrating and testing electronic measuring devices such as multimeters, voltmeters, ammeters, and data acquisition systems. They provide a stable and accurate DC voltage or current source that serves as a reference for verifying the accuracy of measurement instruments.
These calibrators come in various forms, including portable handheld devices, benchtop units, and rack-mounted systems, catering to different application requirements and environments. They are used in industries such as aerospace, automotive, telecommunications, power generation, and electronics manufacturing, where precise measurements are critical for quality control, compliance, and reliability.
How DC Calibrators Work
DC calibrators operate based on the principle of generating precise DC voltages or currents using stable and well-controlled internal circuits. They typically feature high-precision digital-to-analog converters (DACs) that convert digital signals into precise analog voltages or currents. These DACs are calibrated and characterized to ensure accuracy and stability over time and environmental conditions.
Modern DC calibrators often incorporate advanced features such as multiple output ranges, programmable setpoints, voltage and current limiting, and communication interfaces (such as USB, Ethernet, or GPIB) for remote control and automation. Some models also offer built-in calibration procedures and uncertainty calculations to simplify and streamline the calibration process.
Importance of Precise Measurements
Accurate measurements are fundamental to ensuring the performance, safety, and reliability of electrical and electronic systems. In industries such as aerospace and defense, where critical systems must operate within tight tolerances, even minor measurement errors can lead to costly failures or compromises in system functionality.
For example, in aircraft avionics testing, precise voltage and current measurements are crucial for verifying the performance of navigation systems, communication equipment, and flight control systems. Any inaccuracies in these measurements can jeopardize flight safety and mission success.
Similarly, in industrial automation and control systems, precise measurements are essential for monitoring process variables, controlling machinery, and ensuring product quality. A slight deviation in measurement accuracy can result in production errors, equipment downtime, and increased maintenance costs.
Calibration and Traceability
The accuracy of measurement instruments, including multimeters, oscilloscopes, and data loggers, relies on regular calibration against traceable standards. Calibration involves comparing the instrument’s readings to known reference values and adjusting it as necessary to minimize measurement errors.
DC calibrators play a vital role in this calibration process by providing stable and accurate DC signals for verifying and adjusting the performance of measurement instruments. They serve as the reference standard against which the instruments are calibrated, ensuring traceability to national or international standards such as those maintained by NIST (National Institute of Standards and Technology) in the United States or NPL (National Physical Laboratory) in the United Kingdom.
Traceability is crucial for establishing the accuracy and reliability of measurement results across different laboratories, industries, and countries. It provides confidence in the consistency and comparability of measurements, supporting quality assurance, regulatory compliance, and international trade.
Advancements in DC Calibration Technology
Over the years, DC calibrators have evolved significantly in terms of accuracy, versatility, and ease of use. Modern calibrators offer enhanced features and capabilities to meet the evolving demands of industries and measurement applications.
- Improved Accuracy: Advanced calibration techniques, precision components, and temperature compensation mechanisms contribute to higher accuracy and stability in DC calibrators, minimizing measurement uncertainties.
- Multifunction Capability: Many DC calibrators now support multiple functions, including voltage, current, resistance, and temperature simulation, allowing users to calibrate a wide range of instruments with a single device.
- Automation and Software Integration: Integration with calibration software and automation platforms enables automated calibration procedures, data logging, and report generation, reducing manual errors and improving productivity.
- Remote Control and Monitoring: Calibrators with remote control capabilities via Ethernet, USB, or wireless interfaces enable technicians to perform calibrations and monitor measurements from a centralized location, enhancing efficiency and flexibility.
- Calibration Uncertainty Analysis: Some advanced calibrators incorporate algorithms for estimating and analyzing calibration uncertainties, providing users with valuable insights into measurement accuracy and confidence intervals.
Applications of DC Calibrators
DC calibrators are extensively used in various industries and applications where precise electrical measurements are critical. Some common applications include:
- Electronics Manufacturing: Calibrating multimeters, power supplies, and signal generators used in electronic component testing and production.
- Power Generation and Distribution: Testing and calibrating energy meters, relays, and protection devices in power plants and electrical grids.
- Aerospace and Defense: Verifying the performance of avionics systems, radar equipment, and missile guidance systems in aerospace and military applications.
- Telecommunications: Calibrating network analyzers, spectrum analyzers, and communication testers for maintaining telecommunications infrastructure and equipment.
- Research and Development: Characterizing sensors, data acquisition systems, and measurement instruments in scientific laboratories and engineering research facilities.
Conclusion
In conclusion, DC calibrators play a crucial role in ensuring precise measurements across various industries and applications. By providing stable and accurate DC signals for calibrating measurement instruments, these instruments help maintain measurement accuracy, traceability to standards, and confidence in measurement results.
As technology continues to advance, DC calibrators will likely incorporate more sophisticated features, automation capabilities, and connectivity options to meet the growing demands for precision, efficiency, and data integrity in electrical measurements and instrumentation. Engineers, technicians, and scientists can rely on these innovative tools to achieve accurate and reliable measurements essential for quality assurance, compliance, and technological advancement.